We work in an uncertain, competitive economy. To survive, utility contractors need to find new, more efficient ways to streamline their utility trenching projects.
One of many challenges facing contractors might be a lack of manpower. Did you know that between 2003 and 2020 the percentage of construction workers who were age 55 and older went from 11.5% to 22.7%? Unfortunately, only 9.4% of workers are 16-24 years old, leading to a shortage of skilled construction workers.
Other challenges include rising material costs and global supply chain issues. Stricter safety and environmental regulations are an additional consideration. And then there is technology integration. GIS, drones, telematics and field management software provide dizzying options to help with project management.
In today’s world, it’s critical to evaluate your utility trenching for efficiency and best practices. Luckily, new asphalt grinding technology and asphalt cutting methods can keep your project timeline and budget on track.
Asphalt recycling with high-powered asphalt grinding machines streamlines your utility trenching process. To put it simply, grinding asphalt instead of saw cutting cuts time, money, and manpower. Here are five efficiency hacks to help you thrive in today’s conditions.
#1 Ditch Saw Cutting Asphalt for Asphalt Grinding
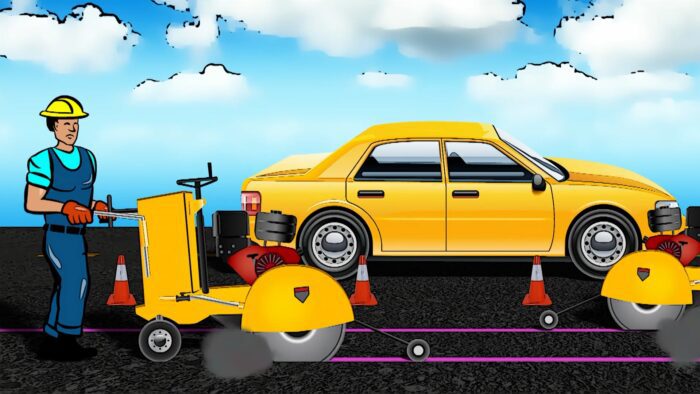
Recent innovations in technology make saw cutting an inefficient and very expensive way to cut through road surfaces. The problem is that saw cutting is only the first step of the process.
After saw cutting, you’re still left with chunking out the asphalt. Then crews load the asphalt chunks into dump trucks to be hauled away for disposal or recycling. This multiple step process involves several crew members and a lot of equipment. This means more people to pay, providing you can find skilled workers, and meanwhile, the clock keeps ticking on your project timeline.
Asphalt grinding greatly reduces or even eliminates the need for cutting, chunking, loading, hauling, and asphalt disposal. With a single pass, the asphalt grinder pulverizes the asphalt into spec-grade reusable material.
Let’s say you have a 400 foot trench that would normally take 8-plus hours to saw cut, chunk, load, haul and dispose. You can now do the same job with an asphalt grinding attachment in as little as 20 minutes. The resulting time, cost, and manpower savings are significant.
#2 Do Your Asphalt Grinding In-House
If you own your own equipment, you don’t have to sub-contract your asphalt removal. This gives you long-term control over your project timeline and budget. With your own equipment, you can open only the trench that you need to work on each day.
This eliminates many traffic control issues and speeds up utility project completion times. Contractors can also transport the same asphalt grinder to multiple job sites in the same day.
#3 Use Your Reclaimed Asphalt Pavement (RAP) as Trench Backfill
An asphalt grinding attachment recycles the existing pavement into reclaimed asphalt product (rap) which can often be used for trench backfill. Using recycled asphalt material is more cost effective and environmentally friendly. It eliminates hauling out old material and hauling in new. It also limits the negative environmental impact of asphalt chunks in landfills.
#4 Find the Right Asphalt Grinder for the Job
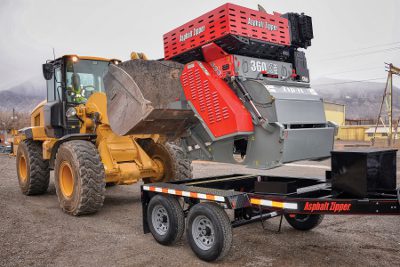
Asphalt grinders come in all shapes and sizes. Depending on your background, you might also call the same piece of equipment an asphalt milling machine or a cold milling machine / cold planer. Options range from skid steer cold planer attachments to large self-contained milling machines.
A cold planer that attaches to your skid steer allows you to grind small sections of asphalt surface. Skid steer milling attachments are quite limited on cutting depth and speed. At the other end of the scale, large self-contained asphalt milling machines have exponentially more production capacity. This expensive equipment can also be difficult to maneuver and require special transportation to the job site.
Many contractors find asphalt milling attachments that connect to a backhoe or loader the sweet spot of asphalt grinding. Contractors pull these machines to the job site behind a regular work truck. They connect to a backhoe or loader in just a few minutes, and their speed and power match that of larger, more expensive machines.
#5 Use an Asphalt Grinder for Surface Milling
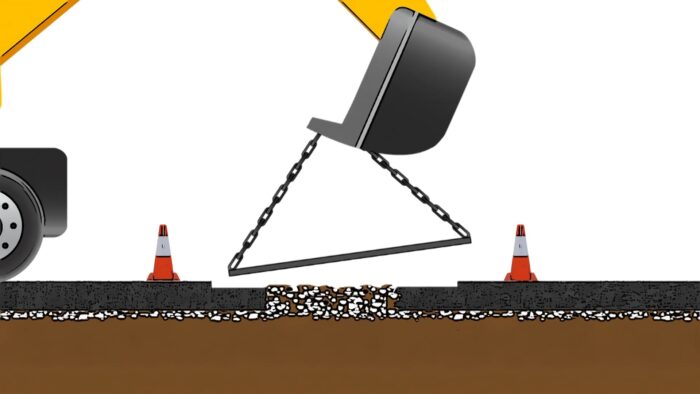
If you are removing asphalt on a utility trench, you are looking to remove the full depth of the asphalt. On the same job, you might also be doing t-cuts and trench plate recessing.
Asphalt grinding attachments equipped with hydraulic cutting depth control can also mill a few inches of the existing asphalt. In other words, it is possible to use one machine for multiple applications on the same job site.
Conclusion
Contractors face labor shortages, rising costs, and more project demands. Because of this, using smarter utility trenching methods is essential.
By upgrading to asphalt grinding technology and choosing the right equipment, you can save time and money. These five efficiency hacks will help your business and set your team up for long-term success in a fast-changing industry.
Key Takeaways
- Replace saw cutting with asphalt grinding to eliminate multiple steps and dramatically reduce project time.
- Choose the right asphalt grinder for your project size and mobility needs—balance power with maneuverability.
- Bring asphalt grinding in-house to gain control over scheduling and avoid subcontractor delays.
- Use one machine for multiple tasks—from full-depth trenching to shallow surface milling.
- Recycle reclaimed asphalt on-site to reduce costs and improve environmental sustainability.