Utility trenching has come hundreds of thousands of miles (literally), from pickaxes and shovels. James Hill developed the first mechanical utility trencher at the Bowling Green Foundry and Machine Co in 1893. He then christened it the Buckeye No 88, marking the beginning of the end of hand-dug trenches.
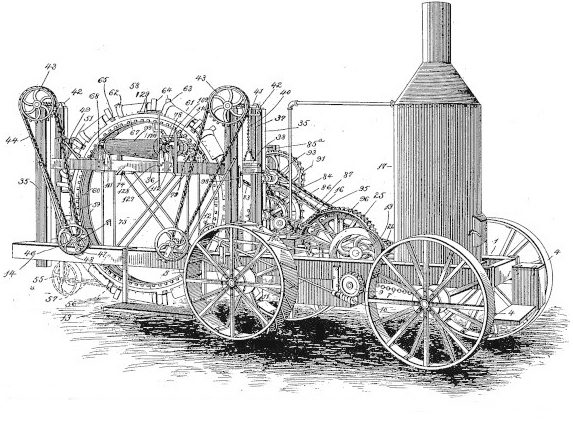
Technology leaped ahead again post WW2 with Ditch Witch’s first trenching machine. Featuring hydrostatic propulsion and a John Deere diesel engine, it quickly made manual excavation virtually obsolete.
Today, even though utility trenching has come a long way, it’s still very cumbersome to remove the asphalt before you can dig your trench. Unfortunately, many utility contractors still use asphalt removal processes firmly fixed in the mid-20th century. This involves all the sawcutting, chunking, loading, trucking and disposal, leaving a trail of budget and time inefficiencies.
Fortunately, there is a superior asphalt removal solution: portable asphalt grinding machines / asphalt milling machines. In the early 1990’s, a contractor observing large milling machines wondered if he could get the same production from a portable milling attachment.
After several prototypes, the early Asphalt Zipper® was born in 1994. This game-changing piece of equipment has evolved and improved over the years, allowing utility contractors to do in minutes what used to take hours or even days.
An asphalt grinder recycles the asphalt into spec comparable road base material which can often be used as pipe trench backfill. With its precision, efficiency, and eco-friendly benefits, asphalt grinding is setting a new standard for utility trenching contractors. Let’s dive into how this innovative method is reshaping the way we think about utility trenching.
The Problem with Traditional Trenching
Conventional trenching methods that use concrete saws for asphalt cutting are far from perfect. They’re often very slow, costly, and the smooth edge can delaminate, leading to uneven surfaces that weaken over time along the trench cut.
Beyond that, traditional trenching generates a lot of waste. The removed asphalt typically ends up in a landfill, adding to environmental concerns. And since only construction and demolition (C&D) landfills accept asphalt chunks, you might be paying excessive hauling and disposal fees.
Let’s also not forget the inconvenience caused by extended job site road closures impacting local businesses and residents. Luckily, there is a detour around these issues, and that’s where asphalt grinding comes in.
What is Asphalt Grinding
Asphalt grinding / asphalt milling uses specialized machines like cold planers, asphalt milling machines, and asphalt grinding machines. These machines have rotating milling drums equipped with carbide teeth that pulverize asphalt and recycle it into spec-comparable base material which can often be used as trench backfill.
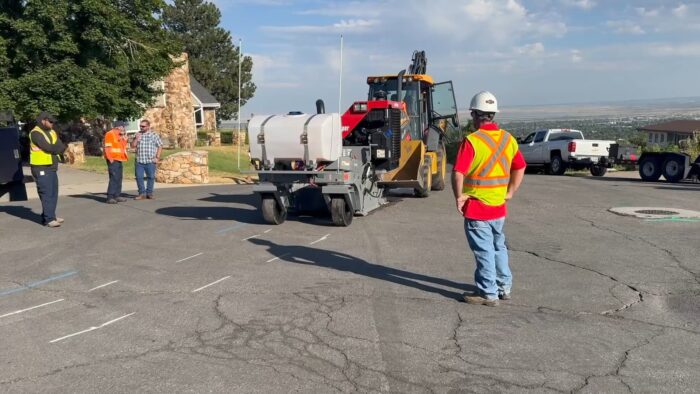
Portable asphalt grinding machines with hydraulic depth controls grind the existing surface to a specific cutting depth and width. Unlike traditional methods, asphalt grinding provides greater control of the asphalt removal process. Asphalt grinders also create unique interlocking edges that bind with the new asphalt to help reduce trench settling.
Portable asphalt grinders are also highly efficient, with power comparable to larger milling machines. You pull them to the construction site behind a work truck, and their smaller size allows them to fit in tight areas, up against curbs, fences and buildings where larger machines cannot grind. Owning your own asphalt grinder gives you the flexibility to open only the trench you need when you need it at your convenience and timing.
Asphalt Grinding is Game-Changing
Speed and Precision
One of the biggest advantages of asphalt grinding is how quickly and easily it removes asphalt. Asphalt milling machines simultaneously cut and pulverize asphalt in a small fraction of the time compared to traditional sawcutting and excavating.
Cost Savings
Utility projects often operate on tight budgets, and asphalt grinding offers a way to save a lot of money. Asphalt grinding requires less equipment, creates spec-comparable trench backfill, and reduces or eliminates asphalt trucking and disposal costs.
Environmental Friendliness
Speaking of recycling, asphalt grinding is a very green and eco-friendly choice. Contractors repurpose the asphalt millings as trench backfill or spec-comparable road base, keeping waste out of landfills. In addition, the milled asphalt can also be sold for gravel road topping.
Reduced Traffic Disruption
No one appreciates traffic delays caused by roadwork. Asphalt grinding speeds up the trenching process, meaning significantly shorter road closures and detours. Cars can also immediately drive over milled asphalt utility trenches, significantly reducing or even eliminating the impact on business and residents.
Looking Ahead: The Future of Trenching
As technology continues to advance, the potential for asphalt grinding grows even greater. In the coming years, we can expect asphalt grinding to become the standard for utility trenching projects. By using an asphalt grinder or cold planer now, contractors position themselves to bid more competitively on projects and win more jobs. They also look to the future by recycling asphalt as trench fill and eliminating or reducing asphalt disposal.