Every underground utility project is a juggling act of conflicting priorities. Being budget conscious is important, but it’s also critical to work smarter and embrace the latest technologies. Producing high quality work matters, but so does completing the project on time. In addition to these priorities, keeping crews safe is essential.
Slow-moving projects aren’t just a money pit—they’re a safety risk. In fact, in the United States, 64% of highway contractors reported vehicles crashing into their work zones in 2024. In 2022, work zone crashes resulted in 801 deaths and thousands of injuries. Clearly, getting the job done quickly and traffic moving is vital.
A generally indispensable step in an underground utility project is cutting and removing asphalt. Using the best equipment and methods make all the difference for the finished product. Let’s break down the most common utility trenching methods and see which one delivers the best speed, safety, and cost savings.
The Old-School Way: Saw-Cutting Asphalt
Saw-cutting asphalt is the go-to method for many underground utility contractors cutting asphalt and concrete. It offers control and precision, but it’s important to understand the major downsides of sawcutting.
First of all, it’s slow. Cutting the asphalt is just the beginning. After that, you have to break it up, a process called chunking, load the chunks into waiting trucks, and haul them away to an asphalt disposal site.
This multi-step process involves extra man-power and equipment, a lot of wasted time, and additional costs. On bigger jobs, projects requiring saw-cutting can eat up hours—if not days—of valuable project time.
And let’s not forget safety. The longer your crew is out there breaking up asphalt and moving chunks, the greater the risk. Every minute you waste exposes your team to traffic. In turn, this increases the chances of a work zone accident.
Self-Contained Asphalt Milling Machines
For bigger construction projects, some contractors turn to large self-contained asphalt milling machines. These cold planers grind asphalt material to a set depth, then transfer the asphalt millings onto a truck for removal. While this sounds good initially, there are plenty of reasons why utility contractors don’t own one.
In addition to their higher price tags, these machines can be heavy, difficult to maneuver, and challenging to transport. You’re also looking at extra costs for lowboys, trucking, and specialized operators. If you do use a self-contained asphalt milling machine, you will probably remove all of your asphalt at once. Because vehicles can’t drive over the trenches after the asphalt removal, this also means more traffic delays.
And unless you have a use for those asphalt millings, you still need to pay for disposal and hauling. If you run a busy underground utility crew, a self-contained cold planer might be more bother than benefit.
The Smarter Choice: Portable Asphalt Grinding
Portable asphalt grinders are robust machines that provide most of the benefits of a self- contained cold planer. However, a portable asphalt grinder is more cost effective, boasting asphalt removal costs of as little as 14 cents / square foot. They can also open a 400-foot trench in approximately 30 minutes and have variable cutting depths of up to 12 inches.
A portable asphalt grinding attachment offers greater speed, flexibility, and cost savings. It does this by avoiding the challenges of saw-cutting and self-contained cold planers. Here’s how:
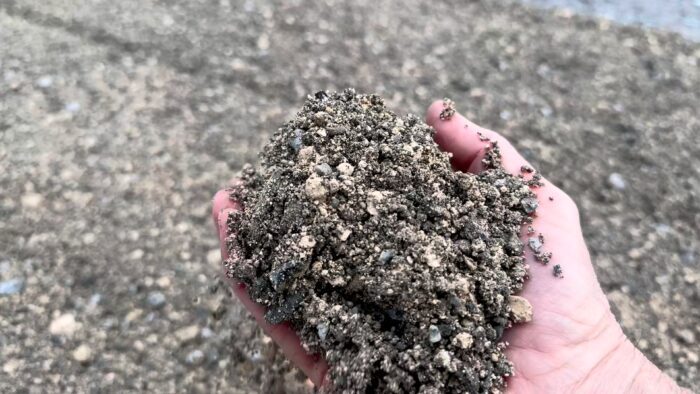
1. Asphalt Recycling Instead of Hauling
A portable asphalt grinder turns old asphalt into spec-comparable recycled material on-site. You may be able to use this recycled asphalt pavement as trench backfill. This can significantly reduce or eliminate your need to haul in new aggregate, and at the same time can eliminate trucking out heavy asphalt chunks or paying high disposal fees. This makes asphalt grinding and recycling an environmentally friendly alternative to saw-cutting and chunking.
2. Easy to Transport
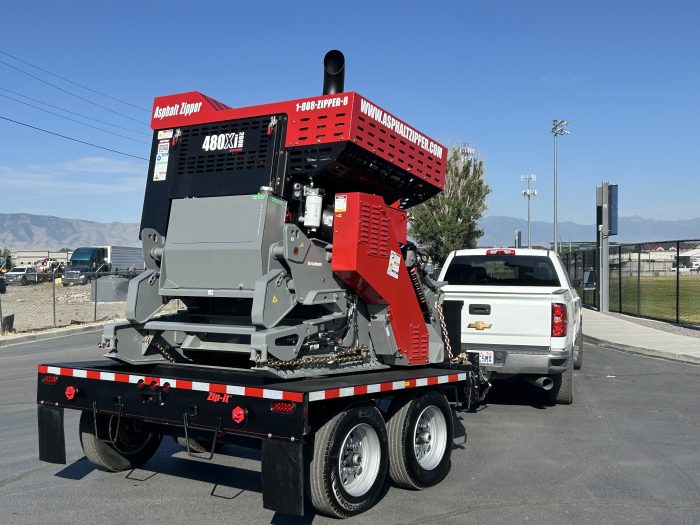
Forget about dealing with oversized loads. You can tow a portable asphalt grinder machine behind a standard work truck. This means no special permits, no waiting for a lowboy, and no hassle.
3. Maximum Mobility
Asphalt grinding attachments connect to a backhoe or loader already on the job site and get to work in minutes. Their smaller size allows them to fit into tight spaces.
This makes these asphalt grinding machines perfect for urban jobs, alleys, and road edges—anywhere you need precision. When you finish for the day, you can simply park them on-site until you need to do more asphalt milling.
4. Increased Safety & Less Traffic Disruption
With a portable asphalt grinder, you can better control your project timeline. You no longer need to wait on subcontractors or shut down long stretches of road.
Instead, you can grind as you go, keeping larger sections of road open for traffic and reducing delays. Plus, cars can drive over the asphalt millings, keeping business access open and your work zone safer for everyone.
5. Get the Job Done Faster
The biggest advantage? Speed. An asphalt grinding attachment can complete a job that used to take all day in as little as 30 minutes. Faster projects mean lower costs and more profit in your pocket.
The Bottom Line: Work Smarter, Not Harder
Using slow, outdated asphalt removal methods wastes time and risks your crew’s safety. A portable asphalt grinding attachment helps you finish your projects on time. It also keeps your team safer by reducing traffic disruptions.
Key Take-a-Ways
- Portable asphalt grinders improve job speed and safety, reducing work zone risks and traffic disruptions.
- Traditional saw-cutting is slow and costly, requiring multiple steps, hauling, and increased crew exposure to traffic.
- Self-contained asphalt milling machines are expensive and difficult to transport, making them less practical for utility contractors.
- Portable asphalt grinders offer cost savings and environmental benefits by recycling asphalt on-site, reducing disposal and hauling costs.
- Portable asphalt grinding attachments are easy to transport and highly mobile, attaching to existing equipment and working efficiently in tight spaces.